I wrote the following article in August 2007. Today is August 9, 2020, and is a special day each year in my life. No, it is not my birthday, but in a very strange roundabout way, it really is…
The article was written for a small ranch land newspaper here in Colorado. It has subsequently been widely disseminated because of the incredible true aviation story it tells about some very good people. This year I thought those of you in the Colorado Pilots Association and your friends would enjoy it as much as others have. You may well know some of the people in it.
My wife Marti and I are thankfully both in good health, very active and leading vibrant lives. But a couple of months ago I stamped 74 years in the time clock of life and realized it does not take much wisdom to look at the calendar and see we have a lot more days behind us than ahead. And in my case specifically, I have a total stranger to thank for all those days, both past and future and he only lived to age 24. That is what the article is about. It involves an airplane that met its demise on this very day, exactly 76 years ago here in Colorado.
Enjoy.
June 6, 1944 is remembered by most as D-Day, the start of the invasion of Europe. But outside of the Pueblo Army Air Base in Pueblo, Colorado, it was also the meeting date of two people who later wed and became my parents. It was on that night while listening to the president’s report of the invasion that Sgt. Chuck Marvel and Val Pritekel were introduced to each other. The person making the introduction was Chuck’s good friend and barracks roommate, Sgt. Harold Humphrey, “Humpy” to his friends. Both Chuck and Harold were Air Corps combat veterans, from the South Pacific and European theaters respectively, and served as radio operator instructors in Pueblo for new B-24 bomber crews in training.
Two months later, on August 9, 1944, Humpy’s B-24 failed to return to the Pueblo base after a routine training mission. The next day it was learned that the aircraft crashed in an open area southeast of Denver and that the entire 10-man crew had perished. War time secrecy and the urgency of training left the accident, one of hundreds across the country during this time frame, as just another quickly forgotten event in history. Chuck asked to be a part of the six-member honor guard that was assigned to escort his friend’s body to his home in New York by train for burial. Harold was an only child and his family was heartbroken. Afterwards, Chuck and Humpy’s parents, as well as Humpy’s favorite uncle, corresponded for years until their deaths.
Less than a year later, on May 1, 1945 Chuck and Val were married in Denver and in a few years my brother and I were born in Kansas City after dad left the Air Corps following the war. As children we knew little of his war exploits but heard the story of how he and mom met. We knew the nickname “Humpy” even though we never had any contact with this deceased airman and no knowledge of his appearance or personality. As we grew up, we learned more of dad’s WWII experiences and actually once saw the foundation of his old barracks while making one of our annual trips to Pueblo to visit our many aunts, uncles and cousins from mom’s side of the family.
In the late 1990s and early 2000s, dad became involved with the Pueblo Air Museum which is at the old air base, now Pueblo airport, and which has a large collection of WWII aviation related memorabilia. In the process of talking about the history of the base, dad mentioned the crash that had killed his friend. No one at the museum had any record of it. The museum staff contacted Larry Carpenter of Estes Park, an “aviation researcher” who has made WWII aircraft accidents in Colorado his hobby for the past 15 years. Larry has extensive knowledge and records but he also knew nothing of this particular accident. Through his contacts in the USAF and with information dad provided, Larry was able to acquire, in 2006, the 15-page accident report on this crash. It revealed that the incident was caused by a fire on the right outboard engine (number 4) and that the right wing failed in flight as a result of that fire. The crew was unable to bail out of the spinning aircraft which impacted in a field “four miles south and four miles east” of the small town of Kiowa, Colorado. Dad sent me a copy of the report and I wondered where the site was and if there was anyone still alive who could identify it. But as with many things on my desk, it just ended up in another pile of papers.
Earlier this year, mom died of cancer in Kansas City a few months before their 62nd anniversary. Dad came out to Grand Junction, Colorado to visit my wife and me in May and then was here a second time in August after attending a family reunion with us near Pueblo. A couple of days before he was to leave and drive back to his home in Kansas City, I asked him what route he was going to take on the return trip. He said he would drive on Interstate 70 because he wanted to go by Kiowa to see if he could find out where Humpy’s plane had crashed. I was taken aback by this not only because I had never heard of that goal but also because dad is now 85, needs a cane or walker to get around following heart bypass and knee replacement surgery and most important, had no clue where this crash site was except “four miles south and four miles east” of Kiowa. I surmised that mom’s death had triggered this latent desire in my dad to locate the site where his friend who introduced him to my mom had died. Marti and I have a home-built RV-8A aircraft that we fly all over the country so I immediately said we would help him. Although the crash site was a 6-hour drive east from Grand Junction, it was only a little over an hour flight for us. We could fly there, help out in the search and then fly back all in the same day. Nice thought, but enter reality. Who would we contact? Were there roads that could take us to the general location of the accident site? Was it a populated residential area, a farm, open range land or what? How would we find the site? If we did find it, was there anything there to confirm it as a place an aircraft had crashed? And most important to me, where was I going to land the plane to meet my dad and his car? But then I looked at my calendar and realized something that motivated me to press on to a solution to all of these problems. In three days it would be August 9, 2007 – exactly 63 years to the day that Humpy died in that crash. In a very real way, his life of 24 years was the basis of mine and my brother’s. Had he not been alive on D-Day to introduce our parents to each other we would not exist. The odds were slim but the timing and the significance of the event were important. I would try my best, realizing that this was a very, very long shot. But what I did not realize then and could not have known was that in the next few days we would meet and be helped by some of the most wonderful people on this planet.
I started by looking at the Denver sectional aviation chart to plot the approximate crash site. I wanted to be able to fly overhead and find the nearest house and a route to drive to it. My initial thinking was that the owner of the land “four miles south and four miles east” of Kiowa may know of the crash site and be able to direct us to it. At least it was a start. But the problem was that even though I could easily do this from the air, I had to land somewhere to meet dad so we could drive to the house I had identified. The sectional chart showed some unpaved runways in the area but my little plane really needed something paved. The only paved runway was at a private strip called Kelly airpark, but this was about 15 miles from the crash site. I had never been to Kelly (or even heard of it) and knew no one there but the Air Nav web site listed a contact name of Frank Niehus. I called Frank and left a message on an answering machine regarding what we wanted to do. A little later, he called back and said we most certainly could land at their private airpark. Furthermore, he said that although he might not be there on August 9, I could call his friend Dick Merring who also lived at the airpark. I had to tie down the airplane somewhere and since there is no transient parking area at Kelly, we needed a home owner who would provide a place to leave the plane. Dick was also very accommodating and explained to me how to taxi to his house and hangar. But the most important question remained. Who knew where the plane crash site was? Neither Dick nor Frank had ever heard of it but they had not lived there that long either. Airparks in general, and this one in particular, did not exist in 1944. But they sensed the significance of our mission and said they were willing to help out if they would be in town. Unknown to me at the time, both had other plans but elected to change those plans to accommodate my goal of helping dad find the location where his friend Harold Humphrey had died exactly 63 years previously.
At some point in a subsequent call I asked Frank the obvious question – was he aware of anyone in the area who lived there in 1944 and thus might have known of the crash. Frank said there was one neighbor on a farm not too far from Kelly Airpark who was “in his 80s” and who was born in the same house where he currently lived. His name was Bryce Gresham and if I could not find his number with the information operator, he would be happy to give it to me when he was back in his house after doing some outside landscaping.
Information had a number for Bryce and I called him. When I did, I was glad I have a strong heart at age 61 because what he said would have floored me otherwise. Bryce is now 80 and distinctly recalls the accident. He was building a silo in 1944 at age 17 and saw the aircraft crash. He was one of the first on the scene and pulled deceased crew members out of the wreckage so their bodies would not burn. Sharp as a tack and still farming every day, he told me very matter of factly, “I can take you to within 100 feet of the crash site.” He also told me that he would be retiring from farming at some future date when he got old! In less than 24 hours I had gone from not having any idea that dad wanted to find the location of Humpy’s final moment of life to locating a man who could take us to the exact spot. But that wasn’t the end of it.
Bryce also told me that the two friends who accompanied him to the crash site, brothers Walt and Marv Maul, also lived in the area and would help us with the search. Keep in mind that not one of these people was a person I knew and this event occurred 63 years ago. All were total strangers to me but every one of them wanted to take part in this effort to help my dad find the crash site and close out a most important question in his life – where is the site where the person who introduced him to his now deceased wife had died? With any luck, we would soon find the answer.
To leave no stone unturned, I contacted Larry Carpenter, the aviation researcher who had acquired the crash report initially in his work with the Pueblo Air Museum. When I told Larry what we were doing, he was excited about it and said he was going to try to alter his own schedule to participate. But he did offer a note of caution that dimmed my growing optimism. It turns out that Larry had contacted Walt Maul on his own last year and had been taken by Walt to the site. Larry had a metal detector and was unable to locate any sign of an aircraft crash. Walt believed the military had completely removed all traces of the wreckage, as did the current owner of the property, Russ McIntyre. The site was in a hay field and had been cultivated many times in the six plus decades since the crash occurred. My hopes were dimmed that dad would be able to take a piece of Harold’s aircraft home with him but we were still going to try. At least we would be in the immediate vicinity of the accident and that would bring a degree of closure to my father.
August 9 dawned bright, clear and calm in one of those classic Colorado days of deep blue skies and unlimited visibility. Marti and I rolled down runway 22 at Grand Junction and climbed to 13,500 feet, passing overhead Aspen and Leadville on the way to our agreed upon 9 AM arrival at Kelly Airpark. When I called in on the unicom frequency, Dick Merring was on the air with his handheld radio and directed me to his home after I landed. Dad had left the prior day and spent the night in Castle Rock. He had a good map showing how to get to Kelly airpark and we were to meet Bryce there also. Shortly after we parked the plane and met Dick Merring, things just started to fall into place. Dad’s car was coming down the road, followed by Bryce’s. Frank Niehus and his wife Lynn pulled in also. We had agreed to meet Larry Carpenter at the ranch owned by Russ McIntyre since Larry had been there before and knew the route to that location. We were right on schedule and departed the airpark for the crash site. Along the way Frank and Lynn pointed out some of the sights in the open, rolling hills complete with beautiful rock outcroppings. They showed us Bryce Gresham’s farm, where he sleeps in the same bedroom where he was born 80 years ago. We saw the silo that Bryce was building when he watched that burning B-24 lose its right wing and spin into the ground several miles to the east. I had a sense that this was going to be a very good day.
When we pulled into the long drive way that led to the McIntyre farm, Marti and I were stunned at all the cars and people there. Seven cars and 13 individuals comprised our group, which also included three metal detectors. Aside from my dad, Marti and me were Frank and Lynn Niehus and Dick Merring from the airpark. The land owner, Russ McIntyre was there, as were Bryce Gresham and brothers Walt and Marv Maul along with Marv’s wife Nancy. Again, Bryce, Walt and Marv were first responders after the crash, braving the flames and explosions to pull several of the deceased crew members out of the plane. In addition, aviation researcher Larry Carpenter and his wife Vi were also there, having driven over two hours from Estes Park to search an area they had already searched unsuccessfully last year. In only a few days we had gone from a seemingly crazy idea to a group of motivated and excited people now all assembled at the same place and at the same time to help total strangers bring about closure for my dad on this quest.
With Russ’s permission to drive into the hay field, we packed into as few cars as possible to minimize damage and drove to a spot near where Bryce recalled the plane being. Bryce drove even closer to reduce the distance my dad had to walk. With no real organization we moved around the general area, both visually looking for any evidence of the crash and using the three metal detectors to scan the ground. Now and then a metal detector would go off but all we found was some old barbed wire and a few rusty nails. We fooled ourselves at one spot thinking there was a large mass of metal in the ground because all three metal detectors were going crazy. After a little experimenting, we realized that the detectors were sensing the other nearby detectors, not aircraft wreckage. During our search, on three occasions different participants pulled me off to the side to thank me for doing this and for letting them be involved. Imagine that – they were there on their own time helping us find this airplane and were thanking me!
Bryce, Marv and Walt had some differences in recollection as to exactly where the plane had come down but none had been there for 63 years so this was not surprising. They pointed out where they first saw it, the direction it was heading, and where some components that came off the plane as it broke up were found along the flight path. But still, we had no evidence of the plane and after an hour it was pretty clear we were not going to find any. Little by little all of the team members gradually moved back to the starting point, thus quietly signaling that our vaunted effort was not going to be rewarded. The last one out in the field was Larry Carpenter, who with his wife Vi had searched unsuccessfully for the plane before.
Not enough can be said in praise of these two. Although neither is a pilot, they use their own time and money to research past crash sites and have amassed an incredible amount of information on accident locations, causes and personnel lost. In some cases they have made contact with relatives of those who perished. If they wish, Larry guides family members who want to close that chapter in their lives to the scene of the crash that killed their loved ones. He and Vi also spend their own money to have bronze plaques made up to mark the date, type of aircraft lost and the names of crew members. For a large crew, these plaques can cost $1000 to have made and installed at the crash site.
Larry had given up on the use of the metal detector and was merely looking at the ground. He had seen many airplane crash sites and knew that it is almost impossible to remove all evidence. He also had the advantage of knowing where he had looked without success previously, and was further away from the starting point than the rest of us. A shout, “here it is!” came from Larry’s direction and we all moved there, about 100 yards from where we had started. The unmistakable evidence of small aircraft parts littered the ground, making the metal detectors unnecessary. Riveted pieces of aluminum, broken segments of heavy cast metal, Plexiglas, parachute snap fasteners, a part of a magneto coil, melted globs of metal and other small pieces of debris were scattered around the area. Since the plane came down in a spin and was not moving horizontally at impact, most of the wreckage was in a small location, a fact confirmed by our three members who had been there 63 years to the day previously. Larry had small colored flags to place at each spot where we found parts, and eventually we placed many of them in a little pile so dad could take what he wanted. He has a photo of his friend Humpy and will have that photo and some parts framed when he returns to Kansas City. Larry also brought a small American flag which we placed in the ground near the components and at his suggestion, held a moment of silence in memory of the 10 men who had died on that very spot in their B-24 so long ago. Dad and his friend had, in a way, found each other on that calm and clear Colorado morning.
Afterwards some of the team had to return home but many joined us for lunch (at dad’s expense!) in nearby Kiowa. We then went our separate ways, but only after I had phone numbers and addresses for everyone. I will be visiting the Pueblo Air Museum to buy B-24 T-shirts for all of the participants and dad will be sending them a copy of his photo of Humpy. With those two tangible mementos and the memory of the occasion, we will all share in the knowledge that we succeeded in doing a really good thing against tremendous odds.
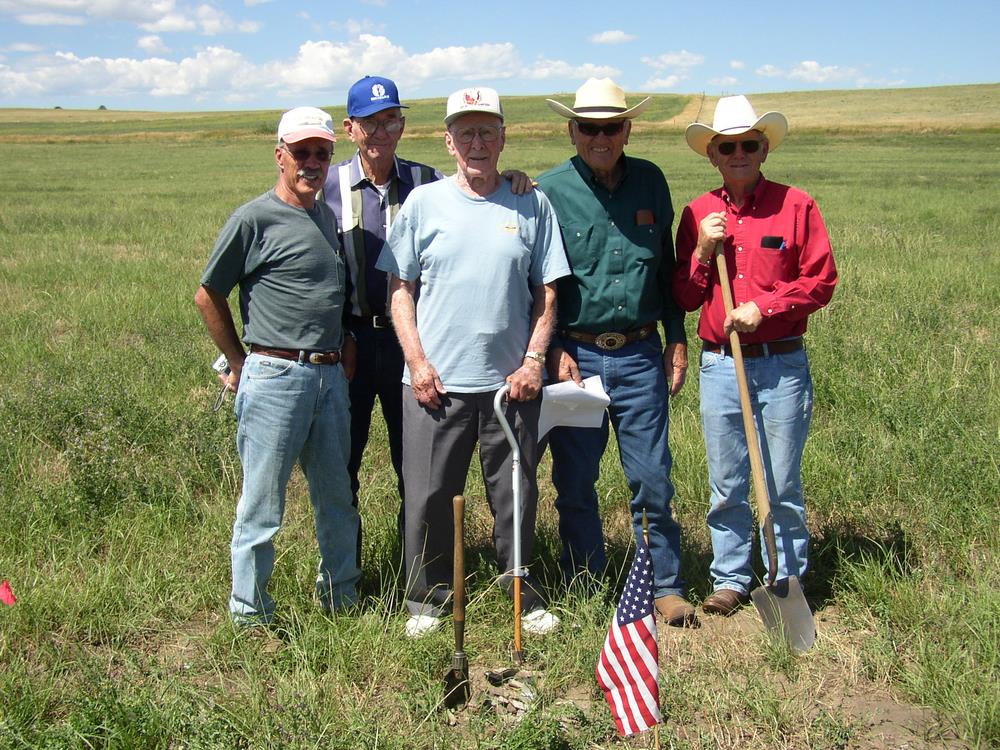
(l to r) Larry Carpenter, Bryce Gresham, dad, Walt Maul and Marv Maul. Bryce, Walt and Marv were all first on the scene after the crash.
Dad holding a piece of the B-24 that his friend died in 63 years to the day previously.
The only photograph of Harold my father had.
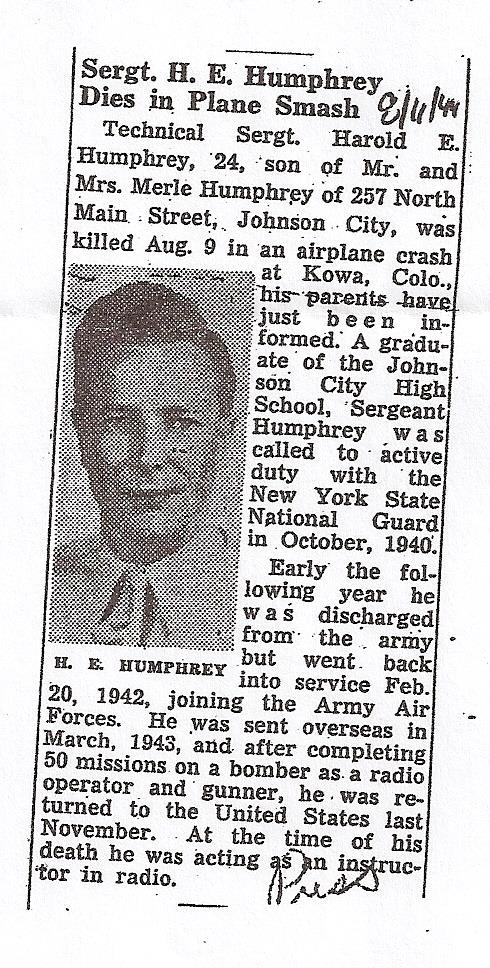
The announcement of his death as printed in the Johnson City, NY newspaper
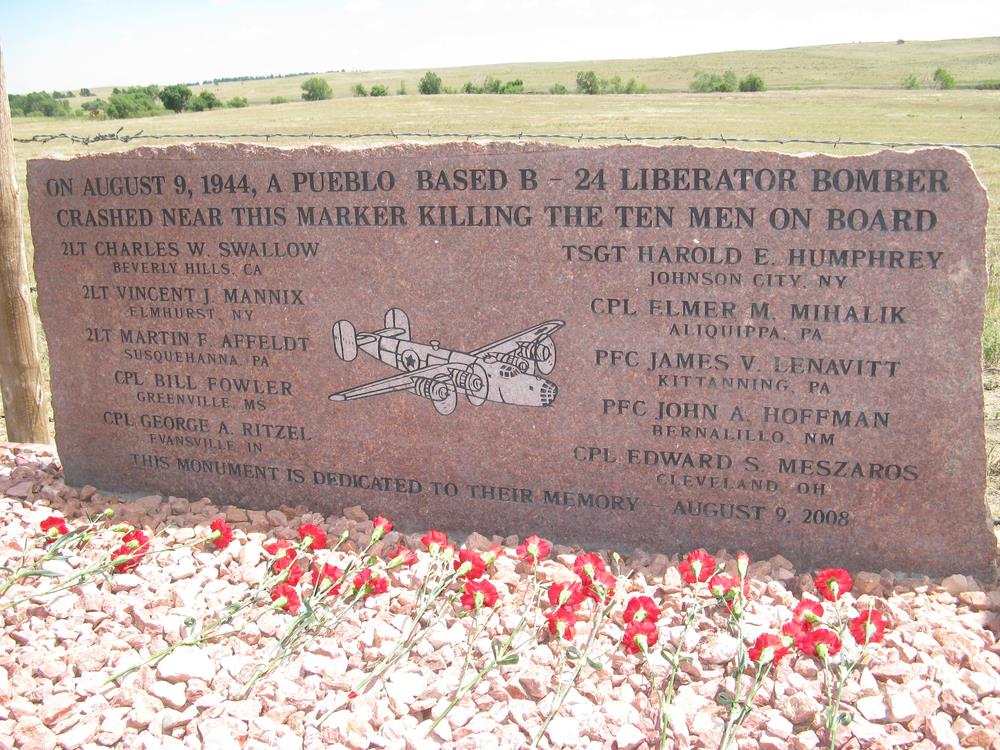
The monument we dedicated at the crash site exactly one year later, on August 9, 2008.
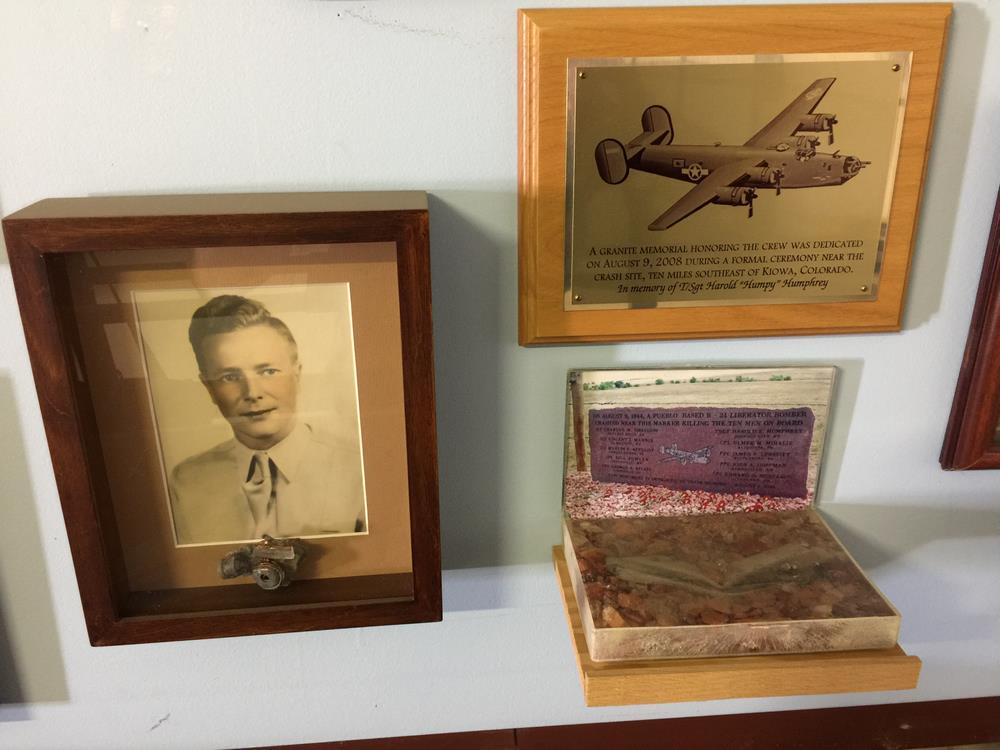
The display dad made up from some of the memorabilia he had and from wreckage we found.
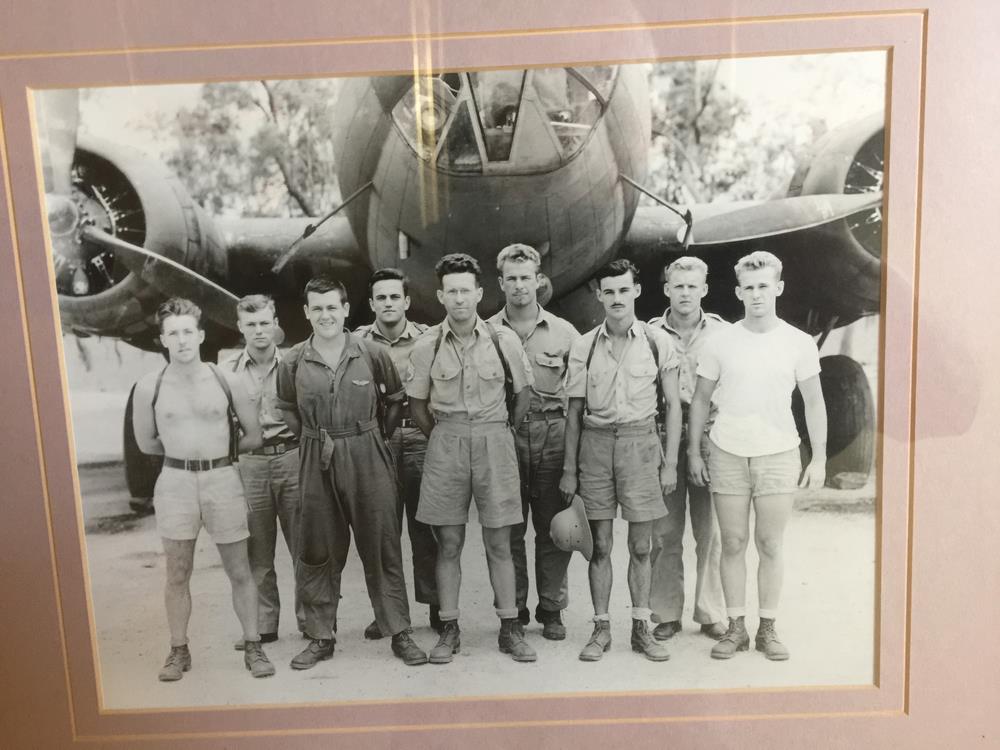
My father is on the far right in the white T shirt. This photo was taken of his B-17 crew in training at Mareeba, Australia before shipping out to the war zone in New Guinea.It was taken on April 23, 1942 and he had just turned 20. He had signed up after Pearl Harbor, took a train from his home in Grand Island, NE to NYC, sailed on a troop ship from there to Melbourne, Australia via the Panama Canal, and was never told where they were going until arrival. Note the guy on his tip toes. That was the aircraft commander, who wanted to be sure he was taller than everyone else! He survived the war only to be later killed in a B-25 crash in Texas. His co-pilot, fourth from the left, was later lost with another crew when their B-17 was shot down over the ocean by Japanese fighters.
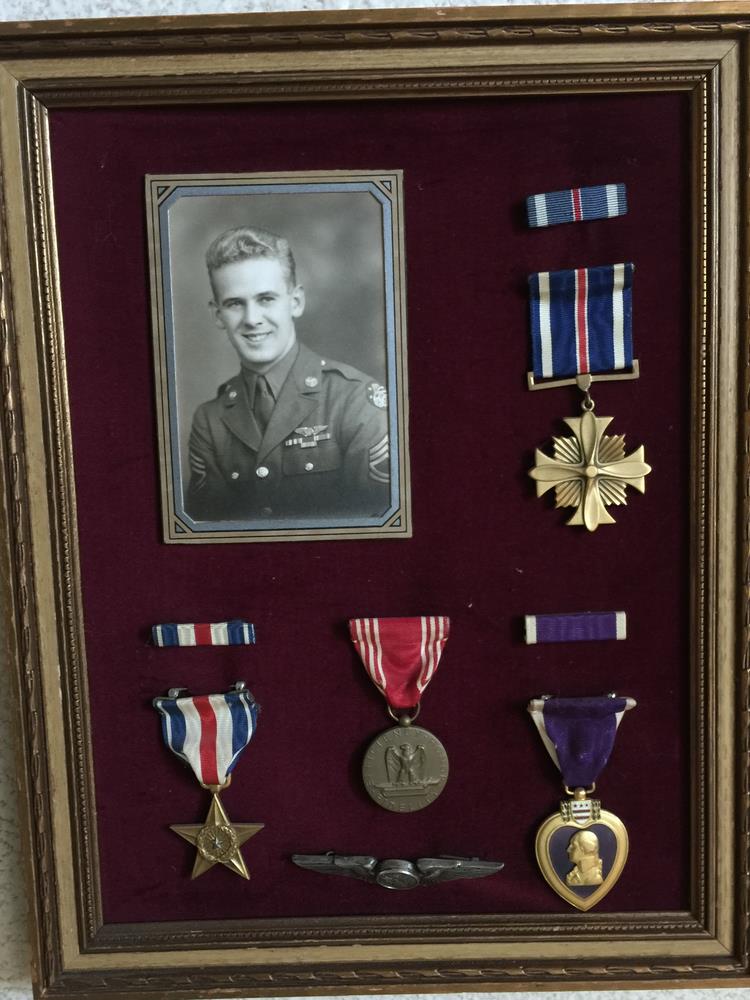
When dad left his small town in Nebraska at age 19, he had never flown in any airplane. He came back a year and a
half later, barely 21, with 43 missions and 300 hours flown against heavily defended targets in places like Wewak, and Lae, New Guinea
and Rabaul, New Britain, all Japanese held areas. He had been awarded the Purple Heart, Distinguished Flying Cross
and Silver Star. When he married my mom on May 1, 1945 in Denver, he had just turned 23.
While the above story is mine, it is only one of many thousands like it. Millions of soldiers and civilians served in WWII and every bit as nobly. Many were just out of high school or a few years older. They gave up everything to save their country and that included some 288,000 who gave their lives, many whose remains were never found. There are very few of these people left now but they are most deservedly called the GREATEST GENERATION.